The birth of high-quality glass bottles requires manufacturers to have good equipment and good glass bottle melting technology.
The design of glass bottle melting furnace and new technology The depth of melting pool of pool furnace depends on the color and viscosity of glass, which is related to the heat permeability of glass. In order to increase the melting amount, it is necessary to reasonably deepen the depth of the melting pool. The depth of the melting pool for colorless glass bottles is generally 0.9-1.5m, and the pool depth of the clarifier behind the kiln is 100-300mm deeper than that of the melting pool. Helps clarify the glass liquid and reduce the temperature of the glass liquid inflow hole, so as to reduce the backflow and prolong the service life of the liquid hole; when melting colored glass, the depth of the melting pool is 0.6 ~ 1.2m, in order to prevent the flow of liquid When the hole is blocked, and the clarifier is 100-300 ram deeper than the melting pool, anti-blocking measures such as electric heating are generally designed before and after the liquid flow hole. In recent years, because pool kilns generally use fuels with high calorific value, which not only increases the melting temperature, but also further deepens the pool depth of the pool kiln.
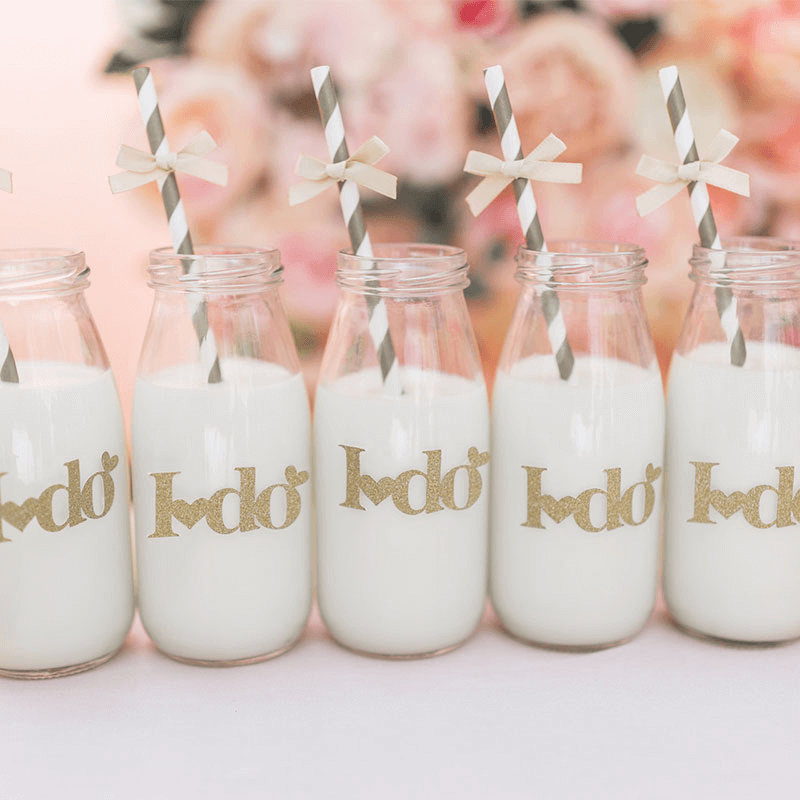
The height of the pool kiln from the factory floor depends on the requirements of various bottle making machines.
In recent years, the production capacity and furnace age of glass bottle tank kilns have been greatly increased, mainly due to the adoption of the following new technologies.
(1) Refractory materials with high physical and chemical properties are used, and each brick is automatically detected online by computer to ensure that the dimensional tolerance of the bricks is as small as possible, so as to avoid fire leakage due to high brick joints in the melting furnace. A new type of unshaped refractory material is used to seal the whole kiln in an all-round way. Zirconium ramming material is used for the pool wall, pool bottom, breast wall and expansion joint, siliceous sealing material is used for the large sill, and light heat preservation is used for the regenerator and flue. coating.
(2) The structure of the kiln has been continuously improved. For example, the flame space of the melting pool and the working pool is fully separated, and the working pool adopts the distribution channel, which is conducive to the automatic control of the temperature system, strengthens the melting, increases the discharge volume, and meets the requirements of the double-drop bottle making machine for a large discharge volume. .
(3) While not changing the shape of the regenerator and saving the cost of the kiln, the form of the lattice body is changed from the Licht type to the cylindrical brick type, which increases the heat exchange area, effectively increases the preheating temperature, and reduces the airflow resistance loss. .
(4) Reasonably place bubbling and kiln sills in the melting pool. The bubbling position is generally set at about 2/3 of the length of the melting pool. Generally, a single row is used, and a double row is also used. A group of bubbling can also be set in the feeding area. The bubbling tube is made of special metal ceramic material, which has good corrosion resistance of high temperature glass liquid. The kiln is set after the bubbling, and the distance between the two is 700-800mm.
(5) The oil gun with a wide range of flame length adjustment is used, which requires low atomization air pressure (normal operation can be performed when the air pressure is ’0.3MPa), the atomization condition is good, and the flame black root is short; increase the distance between the oil guns and expand the flame outlet area to facilitate increased flame coverage and melting and burning. High-efficiency and energy-saving fuel nozzles are used, so that the highest temperature of the flame is concentrated in the chemical material area to achieve enhanced melting of the glass liquid. For example, the DZL type double mixing nozzle from SORG in Germany, the ZL external mixing nozzle from Gaoding Company, the GT/CPA nozzle from Laitlaw Company in the United Kingdom, and the wTPU type extending nozzle from the United Kingdom are all suitable for horseshoe flame kilns and cross-fire kilns.
(6) The use of electric auxiliary heating and oxygen-enriched combustion technology improves the melting rate and achieves the effect of energy saving. Electric auxiliary heating can increase the temperature of deep glass liquid, increase glass output, improve glass quality, and meet the requirements of environmental protection. With oxygen enrichment, the volume of inert gas (nitrogen) is relatively reduced during the combustion process, the volume of flue gas is also reduced, and the heat taken away is correspondingly reduced, resulting in improved thermal efficiency.
(7) The application of the computer automatic control system for the glass melting process plays a role in stabilizing various melting process parameters of the pool kiln, improving the quality of the glass and reducing the consumption of fuel.
In addition to the above items, there are also inclined pool wall bricks for the melting pool wall and a honeycomb vault structure for the large dome roof to improve the radiation ability of the glass liquid and reduce the erosion of the dome roof and the flow of liquid by the alkali vapor. The cave adopts new technologies such as inclined type, which are relatively advanced technologies for saving energy, improving melting quality, and prolonging the service life of the kiln.
The effect of furnace temperature on the uniformity of glass frit: The best furnace temperature control is one of the most important means to ensure high-quality molten glass. Because the furnace temperature control is too low, the formed glass bottle will have burst mouth, insufficient mouth, and even bubbles and stones in severe cases; on the contrary, if the furnace temperature is too high, the liquid flow in the pool will be changed, causing the change of the immobile layer at the bottom of the pool.
Make the glass bottle unclean, produce streaks, and even appear stones, reducing the strength of the bottle. When the furnace temperature fluctuates, first check the change of the entire temperature system, you can check whether the thermocouple is damaged, whether the insertion depth needs to be adjusted due to the burning of the large sill, and the instrument is calibrated. Changes in hot spots due to fuel changes are also a factor that affects melting.